Optimale Fördertechnik: Fehler vermeiden, Leistung steigern
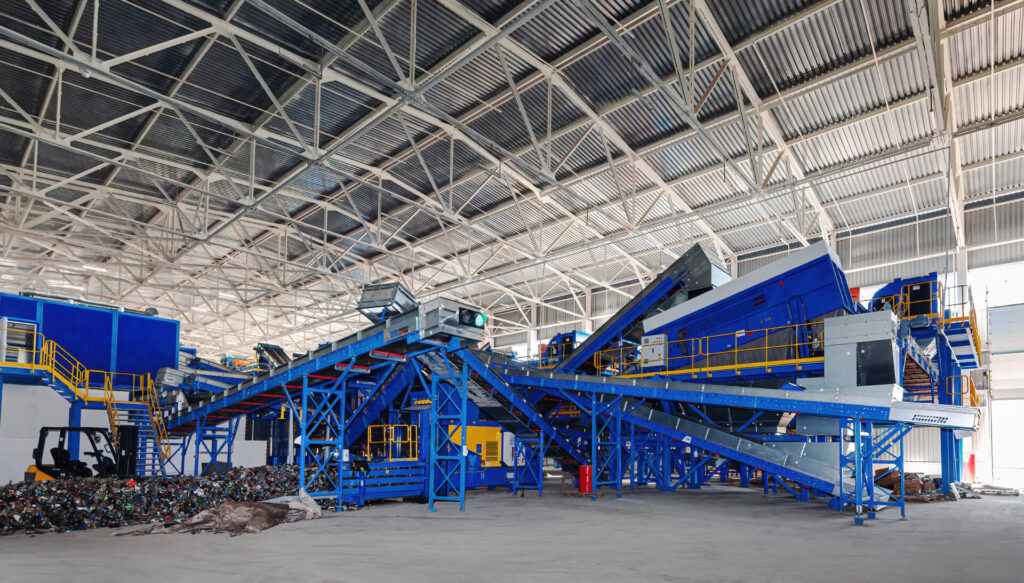
Von Materialfluss bis Verschleiß – so machen Sie Ihre Fördertechnik zukunftssicher
Effiziente Fördertechnik ist ein zentraler Baustein jeder reibungslos funktionierenden Schüttgutproduktion. Und trotzdem: Viele Anlagen verschenken täglich Potenzial – durch schlecht abgestimmte Komponenten, unnötige Stillstände oder unerkannte Schwachstellen im Materialfluss. Die Folge sind steigende Kosten, sinkende Produktivität und unnötiger Verschleiß.
In diesem Fachbeitrag zeigen wir Ihnen, wie Sie durch praxisbewährte Maßnahmen die Leistung Ihrer Fördertechnik signifikant steigern – und gleichzeitig typische Fehler vermeiden. Ob in der Lebensmittel-, Chemie-, Baustoff- oder Kunststoffbranche: Diese Tipps helfen, Ihre Prozesse nachhaltig zu optimieren.
1. Materialfluss ist mehr als Transport
Die Grundlage jeder effizienten Förderlösung liegt im Material selbst. Fließeigenschaften, Korngrößen, Abrasivität, Feuchtegrad oder Neigung zur Brückenbildung – all das beeinflusst, wie gut Ihre Fördertechnik funktioniert.
Typische Schwachstellen:
- Zu geringe Neigungswinkel → Rückstau und Ablagerungen
- Falsche Austragshilfen → Brückenbildung im Silo
- Hoher Verschleiß → ungeeignete Geometrien bei abrasivem Schüttgut
Unser Tipp aus der Praxis:
Lassen Sie den Fokus nicht nur auf der Technik liegen – sondern auf der Anpassung an das Materialverhalten. Ein kleiner Umbau im Einlaufbereich oder eine Vibrationsunterstützung kann oft mehr bewirken als ein teurer Komplettaustausch.
2. Komponenten intelligent auswählen – statt einfach verbauen
Standardlösungen mögen günstig erscheinen, passen aber selten exakt zu Ihrer Produktionsrealität. Zu schwach dimensionierte Antriebe, falsche Dichtungen oder nicht abgestimmte Übergänge führen zu Leistungsverlust und Stillständen.
Häufige Fehler:
- Überdimensionierte Systeme mit unnötigem Energieeinsatz
- Unzureichende Abdichtungen bei staubenden Medien
- Falsche Übergabepunkte zwischen Komponenten
Unser Praxistipp:
Arbeiten Sie mit Partnern, die herstellerunabhängig beraten und praxiserprobte Technik empfehlen. Nur so bekommen Sie Lösungen, die exakt auf Ihre Prozesse, Produkte und räumlichen Gegebenheiten abgestimmt sind – von der Schnecke bis zur pneumatischen Förderleitung.
3. Verschleiß aktiv managen – nicht erst im Ernstfall reagieren
Jeder Betreiber kennt es: Der Förderer läuft – bis er plötzlich nicht mehr läuft. Dabei sind 90 % aller Förderausfälle auf vorhersehbaren Verschleiß zurückzuführen. Und genau da liegt Ihr Optimierungspotenzial.
Typische Risiken:
- Keine regelmäßige Inspektion → unerkannt fortschreitender Verschleiß
- Ersatzteil-Notlösungen → lange Stillstände
- Abrasive Medien treffen auf ungeeignete Bauteile
Unsere Empfehlung:
Setzen Sie auf verschleißfeste Materialien wie Hartmetall, Polyurethan oder Keramik an stark beanspruchten Stellen. Ergänzen Sie Ihre Anlage mit Sensorik zur Verschleißüberwachung – und sichern Sie sich kritische Ersatzteile vorab. So bleiben Sie handlungsfähig, bevor der Stillstand eintritt.
4. Energie sparen durch smarte Steuerung
Fördertechnik läuft oft „einfach durch“. Doch in Zeiten steigender Energiepreise ist das ein Kostenfaktor, der sich vermeiden lässt. Moderne Förderanlagen bieten zahlreiche Stellschrauben zur intelligenten Leistungsregelung – ganz ohne Einbußen bei der Produktivität.
Das sind die häufigsten Effizienzlücken:
- Keine Frequenzregelung → unnötig hoher Grundverbrauch
- Fehlende Rückmeldesysteme → keine Reaktion auf Leerlauf
- Kein Zusammenspiel mit Prozesssteuerung
Unsere Empfehlung:
Nutzen Sie bedarfsorientierte Ansteuerung mit Frequenzumrichtern, kombinieren Sie Sensorik und Steuerung – und reduzieren Sie Ihren Energieverbrauch spürbar. Besonders bei langen Förderstrecken oder variablen Durchsätzen zahlt sich diese Investition schnell aus.
5. Wartung als Teil des Systems denken
Jede Förderanlage ist nur so zuverlässig wie ihre Wartung. Doch genau hier fehlen in vielen Betrieben klare Prozesse, feste Zuständigkeiten und vorausschauende Planung. Die Folge: unnötige Ausfälle und unvorhergesehene Mehrkosten.
Das sehen wir häufig:
- Keine Wartungsintervalle → erhöhte Ausfallwahrscheinlichkeit
- Fehlende Ersatzteillisten oder -lagerhaltung
- Kein Zustandsmonitoring
Besser machen mit System:
Erstellen Sie einen vorausschauenden Wartungsplan, abgestimmt auf die tatsächliche Beanspruchung Ihrer Komponenten. Arbeiten Sie mit einem Partner, der Ersatzteile schnell liefern und Technik effizient wieder in Betrieb nehmen kann. So sichern Sie langfristige Anlagenverfügbarkeit – und Ihre Produktion läuft störungsfrei.
Fazit: Fördertechnik optimieren heißt Prozesse beherrschen
Wer seine Fördertechnik ganzheitlich betrachtet – vom Material über die Mechanik bis zur Steuerung – kann Stillstände minimieren, Betriebskosten senken und die Lebensdauer seiner Anlagen verlängern. Die wichtigsten Stellschrauben: Materialverhalten verstehen, Komponenten exakt auswählen, Verschleiß kontrollieren, Steuerung intelligent nutzen und Wartung strategisch planen.
Bei MT Schüttguttechnik unterstützen wir Sie genau dabei – mit unabhängiger Beratung, robusten Komponenten und durchdachten Systemlösungen, die funktionieren.
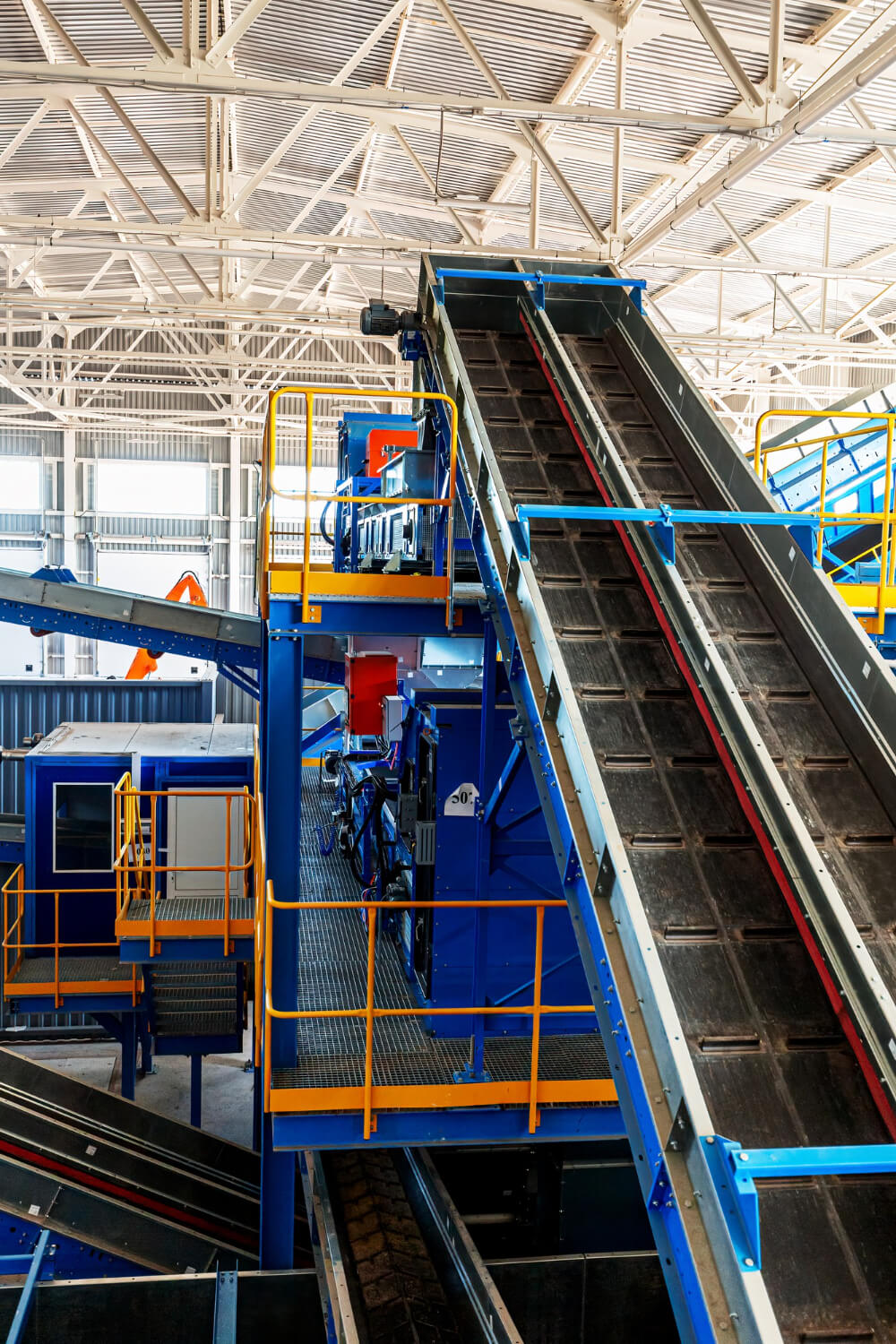
Jetzt das volle Potenzial Ihrer Fördertechnik ausschöpfen
Ob Modernisierung, Erweiterung oder Neuanlage – wir finden die passende Lösung für Ihre Anforderungen. Schnell, praxisnah und ohne Umwege.
- Reduzieren Sie Stillstände.
- Steigern Sie Effizienz.
- Sichern Sie sich unabhängige Fachberatung.